Alignment for 3D Printing Made Simple
SCANLAB GmbH helps demanding users to get more precision, thanks to a software-based 3D Calibration Wizard. This calibration approach lets a scan solution's individual components be aligned step-by-step. Reflecting industry's constantly rising precision requirements of recent years – in 3D marking as well as in additive manufacturing and other applications – this static calibration is a convenient way to attain the most exacting results. Moreover, the dialog-driven software vastly simplifies laser equipment calibration for less-experienced laser machine operators, too.
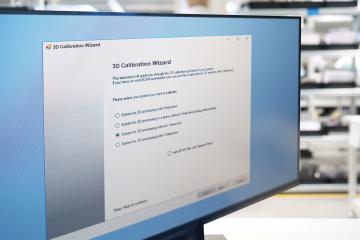
Additive manufacturing is one of the fastest growing areas in a number of industries. These positive developments reflect not only the variety of products currently and potentially manufacturable via innovative 3D printing methods, but naturally also the related laser technology and deployed scan systems. Diverse system configurations can be used, typically in high-performance laser processing machines for additive manufacturing and rapid prototyping, as well as other laser materials processing applications. Here, requirements for accurate calibration obviously increase as more components get integrated into the scan solution. This is exactly where the new 3D Calibration Wizard offers comprehensive support for the daily work of industrial laser processing in optimally setting up and calibrating scan systems.
High accuracy alignment in multiple steps
The new 3D Calibration Wizard enables a maximally accurate individual alignment of all system components – e.g. a 2D scan head combined with an F-Theta objective or z-axis extension – via evaluation of test patterns and marked points. Calibration proceeds step-by-step under the easy-to-understand guidance of the software's dialog windows. Recommended marking parameters are included in a separate correction file. After each step, an individualized configuration file gets generated and automatically loads to take command of the alignment task before the next step is taken. This predefined approach reduces sources of error.
Upon successfully running the entire 3D Calibration Wizard, an individualized system-specific correction file is created to secure maximum processing precision for all applications. Results of the individual steps flow into the final result, thus allowing significant improvements to precision and spot variation. Users receive quantifiable benefits –not just in terms of laser processing and product quality, along with avoidance of rejects – but above all in terms of reduced effort and a vastly simplified calibration procedure.