Process Development for LPBF and Other Laser Processing Systems Made Easy
SCANLAB GmbH is expanding its range of solutions for additive manufacturing (AM) and other fields of application, such as micromachining. The company is presenting various new products at the Formnext show in Frankfurt am Main. Plant manufacturers and laser process developers should above all take a closer look at the feature set of SCANmotionStudio. The new software offers the possibility to develop and optimize new exposure strategies quickly and easily via a graphical user interface. In addition, the trajectory planning and simulation software SCANmotionControl can be integrated and used without any programming knowledge. The new excelliSCAN 30 ARRAY is a particularly flexible and compact scan head that is precisely tailored to the requirements of the AM industry.
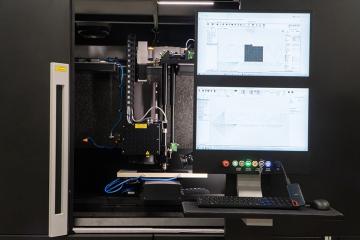
The development of new processing strategies for higher quality and productivity in LPBF systems is time-consuming and complex. With the recently introduced SCANmotionControl control system, the manual optimization of delay parameters on the system that was previously necessary is now a thing of the past. Process developers can simulate the scan paths of the lasers offline on the PC. As the physical properties of the scan systems are taken into account in the simulation, the paths in the application are executed by the machine exactly as in the simulation: 'What you simulate is what you get'.
SCANmotionControl is a programming library that is easy for machine builders to integrate. In order to evaluate the advantages of SCANmotionControl before any integration effort is required, SCANLAB now offers two different solution options for different application scenarios.
Two ways to the optimum exposure strategy
A new software is now available for laboratory tests on an LPBF system. SCANmotionStudio handles the import and slicing of large, complex 3D models, generates support structures and hatch lines and offers the possibility to freely define and vary all laser and scanner parameters for each generated vector. In addition to the classic control of the RTC and support for SCANahead control, trajectory planning with SCANmotionControl is also integrated into the SCANmotionStudio user interface. The simulation function of SCANmotionControl helps users to narrow down suitable process parameters. Processing results can be generated virtually at the touch of a button: The entire system, including sensors and cameras, can be controlled centrally without any programming effort.
SCANLAB is cooperating with suppliers of build processors for AM in order to offer users from the additive manufacturing (AM) sector without laboratory access the opportunity to evaluate SCANmotionControl. SCANmotionControl is now available in Autodesk Fusion & Netfabb, among others. The CAD data of the component can be prepared for 3D printing in the usual way. With the help of the SCANLAB app in Fusion & Netfabb, the specific process parameters can be optimized and the scan path simulation can be calculated, visualized and analyzed for each individual layer. This allows users to evaluate the component-specific benefits of SCANmotionControl in their familiar environment.
New scanning system for 3D printing
There is also a new addition to the scan head range. The excelliSCAN 30 ARRAY was specially designed for the high demands of 3D printing processes. The particularly narrow design makes this system ideal for use in multi-head systems. Thanks to the special mechanical design, several scanning systems can work together in a space-saving manner within one machine with a very large image field overlap, thus significantly reducing process times. The high precision and drift stability required for component processing is ensured by the use of galvanometers with digital encoders.
The excelliSCAN 30 ARRAY is 'ready for SCANmotionControl' and thanks to SCANahead technology, it always works with the maximum possible acceleration, regardless of the scanning speed. Users maximize their laser-on times and shorten process times.