Optimal Control of Laser Processes
SCANmotionControl calculates optimum trajectories from specified machining patterns and process parameters, taking into account the physical limits of the scan head. For example, the tolerable rounding of corners can be defined or a constant process speed can be specified. This achieves an optimum processing result with minimum laser-off times without time-consuming optimization loops.
Benefits
- Highest precision and exact laser control by trajectory planning
- Shortest process time through optimal use of scanner dynamics and laser power
- Advanced Spot Distance Control (SDC) function
- Simple job planning and simulation: 'What you see is what you get'
- Multi-head and multi-instance capability (up to four scanners)
High Precision Laser Control
![]() |
SCANmotionControl enables precise synchronization of the processing path and laser parameters. Assuming a suitable laser, users can specify not only the minimum or maximum process speed, but also the pulse spacing and energy density of the laser spots in relation to their position. The software then calculates the optimum combination of scanner and laser control.
|
Programming and Integration
SCANmotionControl is a dynamic program library (DLL), whose user interface is designed in such a way that existing application programs for RTC6 control cards can be ported easily. The API functions of the SCANmotionControl-DLL allow definition, loading and execution of process jobs, the configuration of system parameters, status monitoring and the use of event callbacks. |
![]() |
For program execution in real time, SCANmotionControl uses the RTC6 control board. |
Simulation
![]() |
SCANmotionContol trajectory planning allows scan path and velocities to be optimized in a simulation environment. The SCANmotionContol viewer allows evaluating the simulation results and displaying the position and dynamic values of the scan head as well as the laser control signals. |
Technologies
Sub Cycle Switching In order to achieve exact positioning and homogeneous energy input for short scan lines with high scan speeds, path-synchronous switching of the laser is crucial. With SCANmotionControl and the Sub Cycle Switchingfunction of the RTC6 control board, that enables up to ten switch-on and switch-off events within 10 μs, such processes can be executed extremely quickly and precisely. |
![]() |
Advanced Spot Distance Control Functions Spot Distance Control (SDC) is an innovative feature of the RTC6 control boards to keep the laser pulse spacing constant along any scan pattern. With a resolution of 64 MHz, SDC triggers laser pulses to maintain the desired In combination with SCANmotionControl, SDC can be expanded to contour-dependent laser control. The constant distance can be aligned either along the centerline of the laser pulse chain or tangential to the workpiece’s side. This means that inhomogeneities or burn-in can be avoided, even on sensitive materials, and a uniform workpiece edge can be achieved. |
![]()
![]() |
Power Ramping |
![]() |
Ready for SCANmotionControl
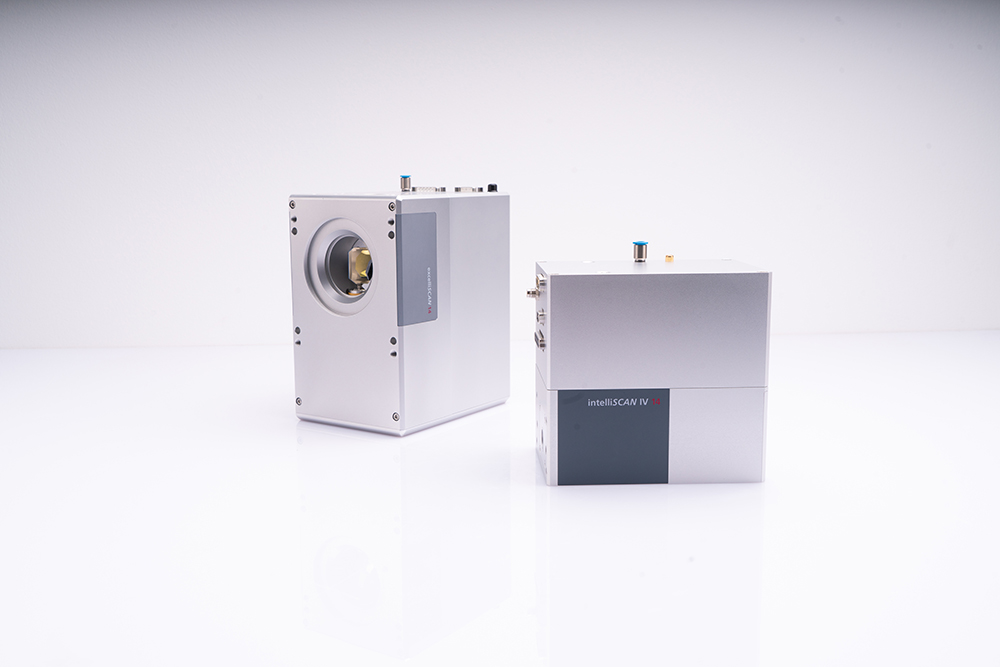
All scan heads of the excelliSCAN- and
The use of SCANmotionControl in existing machine concepts therefore only requires a software adaptation.
Contact us to learn more about the possibilities!
Downloads
Relevant Products
Control solutions for additive manufacturing laser machines by SCANLAB and Autodesk
Efficient operation of industrial laser machines in the field of additive manufacturing requires control solutions that map the entire software landscape from CAD/CAM to machine software right through to laser job execution. SCANLAB works with several providers to deliver suitable solution modules to integrators.